- There is no forming energy unevenness because of the flywheel direct drive by servo motor.
- Replace parts is only V-belt since it is not friction drive. Frequent replace of Friction leather belt is not the case for this machine.
- High speed approach and small power pressing can be programmed to meet high productivity. this machine can cover wide capacity range from small to big size.
- Since it is direct, clutch movement and electric delay for solenoid valve is not developed. High efficiency running by quick response can be operated.
- Static load of 20% nominal capacity can be generated to widen the machine usage, such as straightening or trimming just after forging.
- After one stroke, brake action is made by servo motor by self. Mechanical brake is equipped for the purpose of only emergency. So the brake lining is not subject to wear.
- Slide lower position setting is made automatically during mold setting period.
- The motor is not required to revolve all the time so energy consumption is not so much in spite of the motor size. Energy saving is made by generated return electricity by braking period.
- The absence of lower dead point, it can be pressed several times for the same work by deferent power. It can be performed incremental forging by automatic upper mold shifting device. Frame extension is not subject to thickness unevenness for the pressing work and thin material forging is most favorable work for this machine.
- Acceptable capacity is two times for the nominal capacity. It is possible to give 2 times of nominal force to the frame repeatedly.
- Forming speed can be adjusted to meet the easy forming condition adjustment such as magnesium hot forging.
- High speed forming can be performed. It is most favorable to Hot and Warm forging to prevent the material temperature reducing.
- Cored forging device, semi closed die device, upper mold sifting device and Digital load gauge, safety device, automated device also fully automated program support will be offered on the request.
|
|
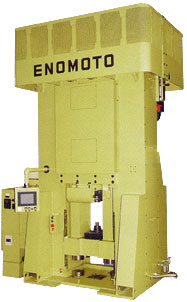 |
|